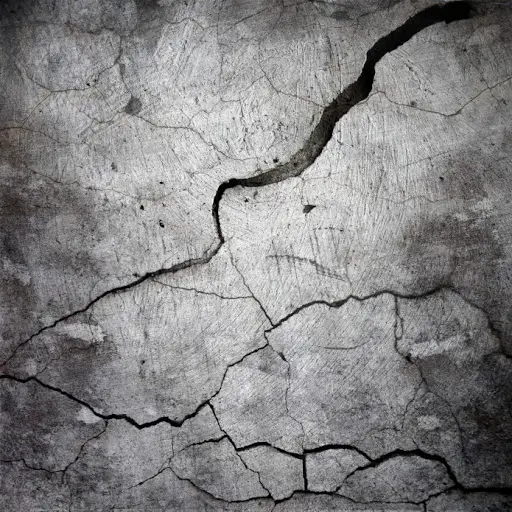
Self Sealing Concrete Using Superabsorbent Polymer
Concrete throughout its life passes by many phases and changes, starting from initial shrinkage from hydration to serviceability hair cracking after loading. Concrete has countless advantages with no-doubt at all and is the reason why it is the second most widely used material after water.
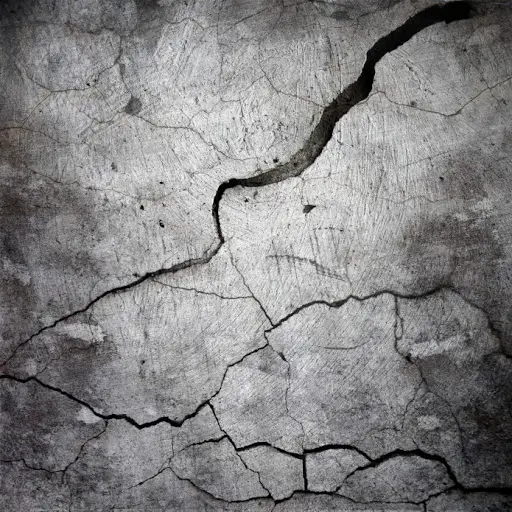
During these phases the concrete also go through cracking which is not visible and perceptible with naked eye however, such concrete if meant to retain water will surely show seepage and water loss which is not desirable.
Concrete after placement and curing within 28 days achieve the most of the strength, however just after the application of the service load like bending the concrete on its surface have cracks which reduces the effective resistive area. This phenomenon is also considered in the design.
However for water retaining structures, this can never be allowed to happen as the concrete and the structure will surely be failed. Concrete with low water cement ratio is found to have less formation of cracks and thus low permeability is observed.
However in otherwise cases the permeability is sufficient which is not acceptable. Some of the cracks of the concrete can self-heal over a long period of time due to several mechanisms including the formation of CaCO3 (Calcium Carbonate) and mechanical blocking by eroded cement particles.
However, this self-healing is limited to cracks of up to 260 – 300 micro meter, and is always not reliable, of course.
In such a situation recently a research has been made by scientists in the field of materials by using a polymer called Self Absorbent Polymer (acronym SAP).
Superabsorbent Polymers also termed as Slush Powder has the capability to retain and absorb extremely large amounts of liquid as compared to their own mass and weight.
The ability of SAP to absorb water depends on the factor of iconic concentration of aqueous solution. If the water is clear deionized and distilled the Super absorbent polymer might absorb as much as 300 times water of its own weight but if some saline solution like sodium chloride is fed than it can only absorb around 50% of its own weight.
If this superabsorbent polymer is used in concrete as admixture than it can self-heal the cracks and reduces the permeability up to large amount of extent. As already mentioned that the swelling capacity changes significantly with the iconic content of the solution. When added to a concrete mix, SAP absorbs about 3-20 grams of water per gram of SAP and swells only slightly. When the concrete sets and hardens, the SAP gradually releases its absorbed water and collapses. The SAP lies dormant in the concrete until cracking occurs that exposes the SAP. If the cracked concrete is subjected to external wetting by a dilute aqueous solution, much more significant swelling of the SAP occurs hence sealing the crack.
In this regard Hong S. Wong of Imperial College London have made a research in which he uses cement pastes and mortar specimen containing 5% Poly Acrylate or 4% Poly acrylate – co-acraylamide as SAP.
Special shape specimen of concrete cylinder were casted having grooves within it which were used afterwards for cracking the specimen. A single through crack of around 100 to 400 micro meter was induced in each specimen. The flow rate of dilute sodium chloride solution through the cracked specimen was measured and results were compared with control specimen which did not have SAP.
Hong S. Wong and his team have found that cumulative flow through specimens containing SAP was significantly lower than for the control. The results suggest that Poly(acrylate-co-acrylamide) is more effective than Poly (acrylate) for crack sealing. Results also showed that larger SAP particle size is more beneficial for sealing cracks.