When it comes to concrete with a large ratio of aggregate to cement; one of that type is dry lean concrete or (DLC). DLC contains pretty less amount of cement paste when compared with conventional concrete. The word “lean” in the Dry Lean Concrete shows that it has more aggregates rather than cement or binding agent.
It is plain concrete that doesn’t have any reinforcement and is widely used in rigid pavements over sub-base course. It has a low slump value so that means you need to compact it with the help of mechanical means.
So, in the mix-design for DLC, aggregate-to-cement ratio plays a critical role. But the recommended maximum value of aggregate-to-cement ratio is 15:1. Anyhow as per the IRC SP-49 1998 specification; the typical thickness of DLC must be between 100 to 150 mm.
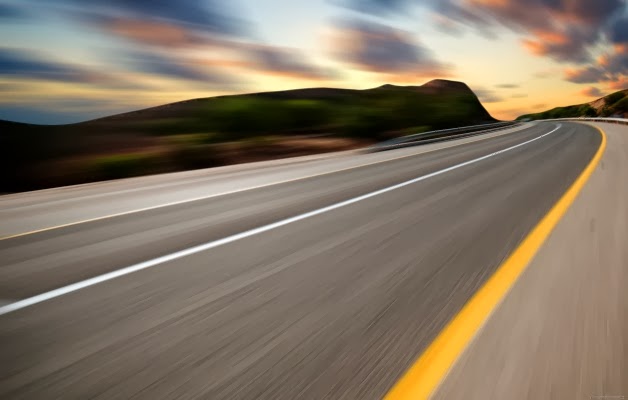
Materials and composition
Construction of a durable layer course (DLC) requires the use of specific types of cement and aggregate materials. The following subheadings will provide more information about the materials that are used in DLC construction and how they are obtained.
Cement for DLC
Ordinary Portland cement, Portland Pozzolana Cement, or Portland Slag Cement can be used for DLC construction. These types of cement are chosen for their durability and resistance to wear and tear.
Coarse Aggregate
Coarse aggregate is a granular material, typically made of crushed stone, gravel, or slag. To ensure the strength and durability of the DLC road, the coarse aggregate should be clean, hard, strong, dense, non-porous, and durable. It should be free of pieces of disintegrated stone, soft, flaky, elongated, very angular or splintery pieces. The maximum size of the coarse aggregate should be 25 mm.
Fine Aggregate
Like Us on Facebook!
The fine aggregate, which is added to the DLC road to fill any voids between the coarse aggregate particles, should consist of clean, natural sand or crushed stone sand or a combination of the two. It should conform to IS : 383, and be free from soft particles, clay, shale, loam, cemented particles, mica, organic and other foreign matter.
Subscribe Us on YouTube!
Obtaining Aggregates
There are two ways to obtain coarse and fine aggregates for DLC construction:
(i) In separate nominal sizes of coarse and fine aggregates and mixed together intimately before use.
(ii) Separately as 25 mm nominal single size, 12.5 mm nominal size graded aggregates – and Fine Aggregate of crushed stone dust or sand or a combination of these two. This method uses a combination of different aggregate sizes for added stability and smoothness in the road surface.
Overall, it is important to use the right materials for DLC construction to ensure the strength and durability of the road surface. The use of specific types of cement and aggregate materials, as well as proper mixing and compaction techniques, contribute to the overall performance and longevity of the DLC road.
Also Read: Concrete Footing Calculator (Isolated – Strip – Raft – Combined Footings)
Specification
- Clean water for mixing and curing of concrete is essential for the finished concrete to be free from harmful substances.
- The mix should be proportioned with a maximum aggregate cement ratio of 15:1.
- The minimum cement content is 150 kg/cu.m. of concrete.
- The average compressive strength of each consecutive group of 5 cubes made should not be less than 10 MPa at 7 days.
- The batching plant should be capable of proportioning the materials by weight, with each type of material being weighed separately.
- Mixing and batching should be done in a forced action central batching and mixing plant, with necessary automatic controls to ensure accurate proportioning and mixing.
- Weighing scales should be calibrated and have an accuracy of ±2% for aggregates and ±1% for cement and water.
- Plant mix lean concrete should be discharged immediately from the mixer, transported directly to the point where it is to be laid, and protected from the weather during transit.
- Lean concrete should be laid/placed mechanically/manually in one layer in an even manner without segregation.
- The laying of the two-lane road sub-base may be done either in full width or lane by lane, with lean concrete being placed and compacted across the full width of the road, by constructing it in one go or in two lanes running forward simultaneously.
Also Read: Concrete Slab Calculator – Calculate Volume of Concrete in a slab and Mix ingredients