Concrete is the second-most used material on the planet, surpassed only by water. This dull, grey substance is essential for constructing homes, hospitals, airports, dams, and much more. It has facilitated humanity’s ability to conquer the underground, providing safe passage for trains, and routes for water, waste, electricity, and internet services. The modern world, as we know it, would be hard to imagine without concrete.
However, concrete is widely considered the most destructive material on Earth. The damage caused by concrete is not just about its ability to entomb vast tracts of fertile soil, constipate rivers, and choke habitats, as Guardian journalist Jonathan Watts once wrote. It’s also about the emissions generated during its production.
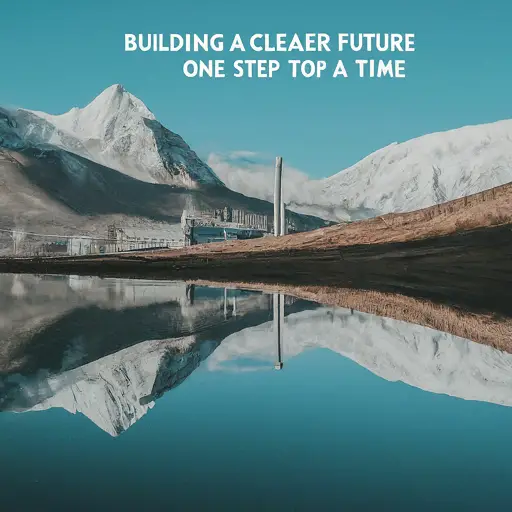
The Carbon Footprint of Concrete
Concrete production accounts for between 7 and 10% of all CO2 emissions, depending on who you ask. The majority of these emissions come from a single ingredient of modern concrete: Portland cement. To make it, you pulverize limestone, silica alumina, and iron, mixing them together in specific proportions. The mixture is then heated in a kiln at temperatures up to 1650°C (~3000°F), releasing CO2 from the limestone and producing a lumpy mixture of stable compounds called clinker. This clinker is cooled, pulverized again, and mixed with a small amount of gypsum. The resulting fine powder, Portland cement, effectively acts as the ‘glue’ in concrete. Efforts to decarbonize concrete mainly target this carbon-rich ingredient, aiming to alter its chemistry without compromising performance.
A Step Towards Sustainability: Sustainable Practices In Pipeline Condition Assessment Training
Environmental Impact of Concrete Ingredients
Concrete’s other two main ingredients also impact the environment. Most of its volume is aggregate – sand, gravel, or crushed stone quarried from mines. About 7% is water. Small quantities of other additives are included to fine-tune the mix. Through a process called hydration, the cement powder and water react, hardening and binding the aggregates and additives into the tough, rock-like mass we’re all familiar with. This hardening process continues for years after the concrete is poured, meaning it gets stronger as it ages, at least for a while.
Given the ubiquity of concrete and its ever-increasing carbon footprint, the race is on to find better, less damaging ways to make it. In the past fortnight, two different approaches reported in the scientific literature have caught significant attention.
Also Read: Evaluating the Impact of Material Selection on Civil Engineering Project Costs and Sustainability
Replacing Cement with Coal Waste
Researchers at RMIT University in Melbourne, Australia, have developed a method to replace 80% of the cement in concrete with a waste product from coal-fired power plants. Burning coal produces staggering amounts of greenhouse gases and other pollutants such as heavy metals. It also leaves behind a fine powder called fly ash, mainly composed of silicon, oxygen, aluminum, iron, and calcium. For every four tons of coal burned, approximately one ton of fly ash is produced, making it a significant waste product. According to RMIT, fly ash accounts for nearly a fifth of all waste in Australia and will remain abundant for decades, even as the country shifts to renewable energy.
The team, led by Dr. Chamila Gunasekara, is not the first to propose using fly ash as a partial substitute for Portland cement. Products using up to 40% fly ash are already on the market, with some achieving 60% but producing weaker, less durable concrete. By adding nano silica and hydrated lime to their fly ash, the RMIT team produced concrete with 65% and 80% cement replacement. Their concrete increased its strength over 450 days and could withstand exposure to sulfuric acid and sulfates found in acid rain for up to 24 months. They also developed a mathematical model to understand how various ingredients in ‘low-carbon’ concretes behave. Dr. Yuguo Yu, one of the study’s authors, stated that this offers opportunities to reverse engineer and optimize mixes from numerical insights. For example, the inclusion of ultra-fine nano additives significantly enhances the material by increasing density and compactness.
Like Us on Facebook!
This work has also allowed researchers to utilize an even lower-grade waste material called ‘pond ash,’ potentially opening a whole new underutilized resource for cement replacement. Gunasekara noted that these ash ponds risk becoming an environmental hazard, and the ability to repurpose this ash in construction materials at scale would be a massive win.
Subscribe Us on YouTube!
Also Read: Types of Cement Grades (33, 43, & 53)
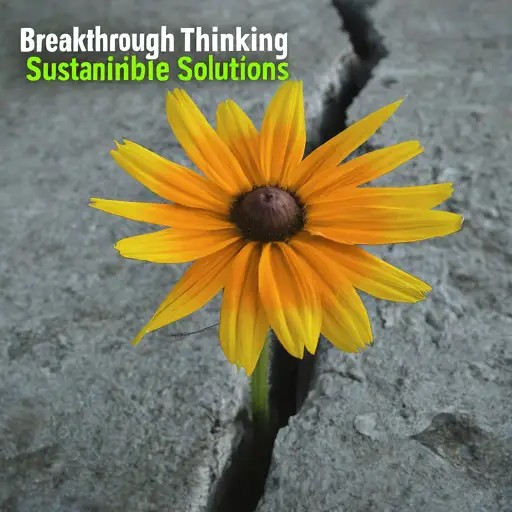
Electric Cement: A Path to Carbon-Neutral Concrete
The second breakthrough comes from engineers at the University of Cambridge, who have developed a method that combines steel recycling and cement recycling. This process uses waste concrete from demolished buildings, separating the aggregate and leaving behind a cement paste (cement + water). This recovered cement paste is then used in an electric arc furnace during steel recycling, replacing lime-flux.
In standard steel recycling, lime-flux forms a coating on the surface of the steel as it melts in the electric furnace, protecting the liquid metal from oxygen in the air. Once the steel is released from the furnace, the coating, now called slag, cools quickly and is crushed into a powder, often sent to landfill. By using recovered cement instead of lime, the Cambridge technique changes the equation. Dr. Cyrille Dunant, who invented the process, found that the combination of cement clinker and iron oxide forms an excellent steelmaking slag because it foams and flows well. Additionally, the heat of the furnace reactivates the cement, turning old, deactivated cement into new, ready-to-use cement.
Dunant and his colleagues, Dr. Pippa Horton and Professor Julian Allwood, have filed a patent application on their process and founded a company called Cambridge Electrical Cement (CEC) to bring it to market. Recent successful trial melts carried out in a 7-tonne electric arc furnace at the Materials Processing Institute demonstrate that the process is scalable. Long-term, the furnace could be powered by renewable energy, effectively reducing the carbon footprint of the process to zero. Patricio Burdiles, CEC’s senior project manager, stated that their reactivated Portland cement is carbon-neutral since there are no process emissions, none from burning fuel, and potentially none from running the electric arc furnace beyond those already involved in recycling steel.
Conclusion
These innovative approaches represent significant strides in reducing the environmental impact of concrete. As the race to find sustainable construction materials continues, these breakthroughs offer hope for a future where concrete’s benefits are not overshadowed by its carbon footprint. For more detailed information on the environmental impact of concrete and the latest research in sustainable construction materials, visit The Guardian and Forbes.