Concrete is a common building material due to its strength, durability, and inexpensive cost. To minimize potential risks and costly repairs, it is critical to assure the quality and dependability of concrete buildings.
Non-destructive testing (NDT) of concrete is one of the finest techniques to do this. NDT is a way of testing concrete constructions that do not cause damage or destruction to the material. The goal of NDT is to identify the structural strength and condition of the material, as well as to determine the integrity and quality of the concrete.
There are various methods of NDT for concrete, including:
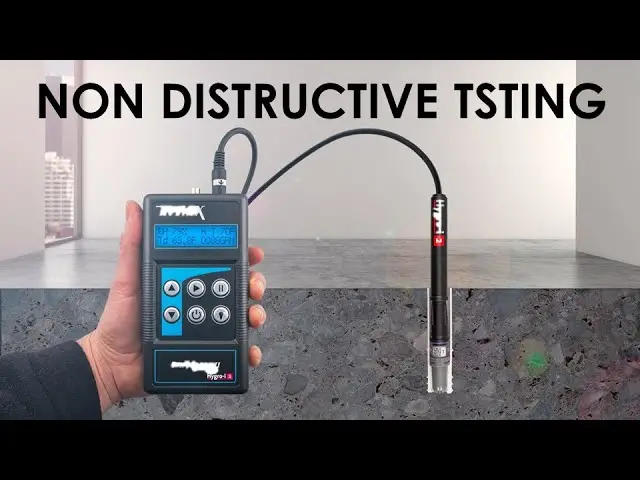
Ultrasonic Pulse Velocity (UPV) Testing:
UPV testing is a popular NDT procedure for concrete. It works by detecting the speed of an ultrasonic wave as it passes through a material. An ultrasonic pulse is fired into the concrete, and the time it takes for the wave to pass through the material and return to the surface is measured. The wave’s speed is related to the density and elasticity of the concrete, and any fractures or imperfections in the material will slow it down, resulting in a decrease in reported velocity. This decrease in velocity may be utilized to detect the existence, location, and magnitude of any concrete flaws.
Also Read: Concrete testing by Ultrasonic Pulse Velocity (UPV)
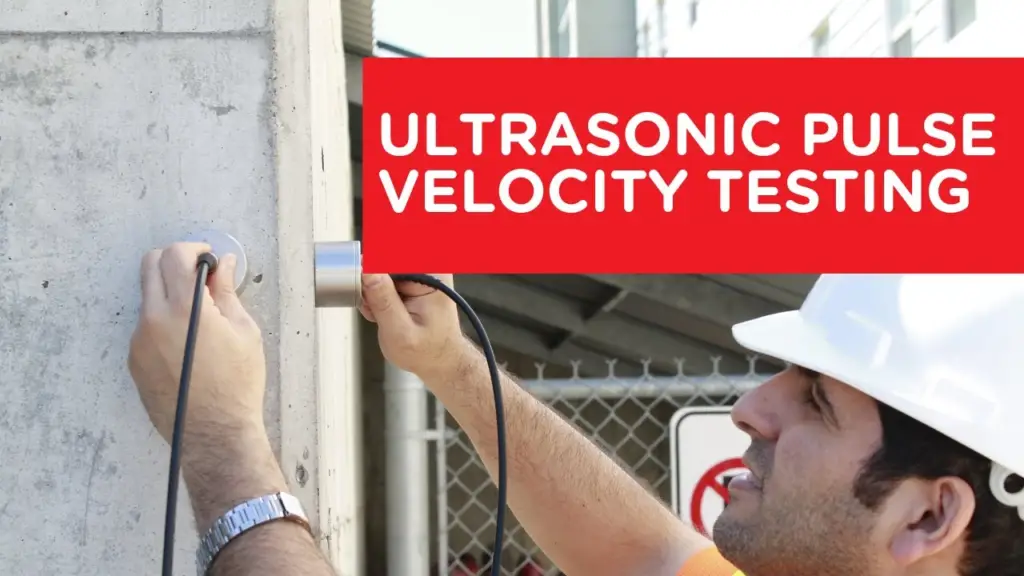
Rebound Hammer Testing:
Another frequent NDT method for concrete is rebound hammer testing. It works on the idea of measuring the rebound of a hammer when it strikes the concrete surface. The hammer’s rebound is related to the hardness and density of the concrete, and any fractures or faults in the material will lessen the hardness, causing the rebound to decrease. This reduction in rebound may be utilized to identify the existence, position, and extent of any concrete faults.
Also Read: How to get burn marks off Concrete? (Simple 5 steps)
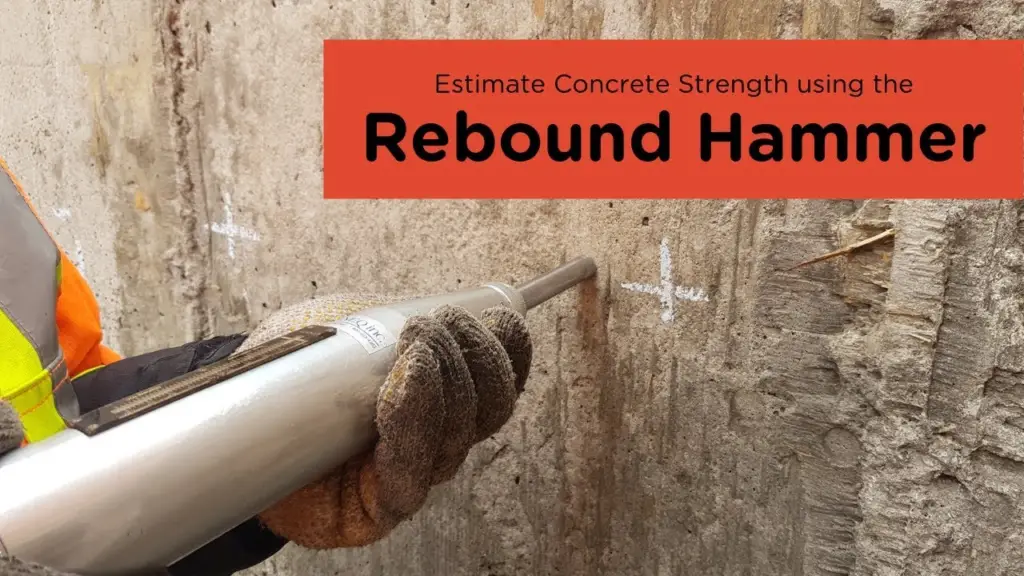
Ground Penetrating Radar (GPR) Testing:
GPR testing is a relatively recent approach of NDT for concrete that is based on the premise of scanning the concrete structure using radar. A radar signal is sent into the concrete and the time it takes for the signal to return to the surface is measured. The signal’s speed is related to the concrete’s density and elasticity, and any fractures or defects in the material will create a reflection in the signal, which may be used to detect the existence, position, and extent of any faults in the concrete.
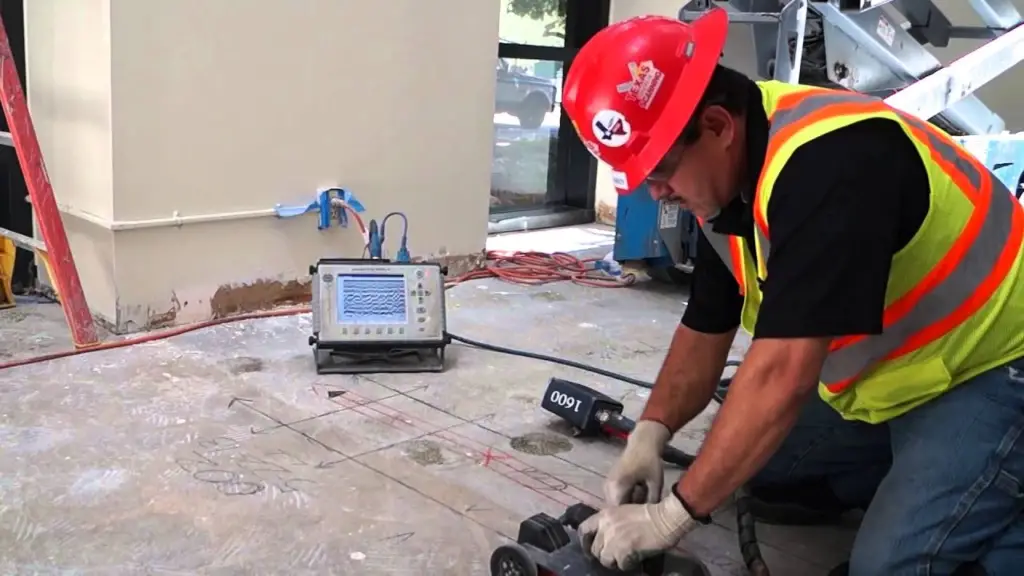
Impact Echo Testing:
Impact echo testing is a nondestructive testing (NDT) method for concrete that is based on the premise of detecting the echoes created by an impact on the concrete’s surface. The test consists of hitting the concrete surface with a hammer and measuring the time it takes for the echoes to return to the surface. The speed of the echoes is related to the density and elasticity of the concrete, and any fractures or defects in the material will result in a decrease in speed, which may be used to detect the existence, position, and extent of any faults in the concrete.
Like Us on Facebook!
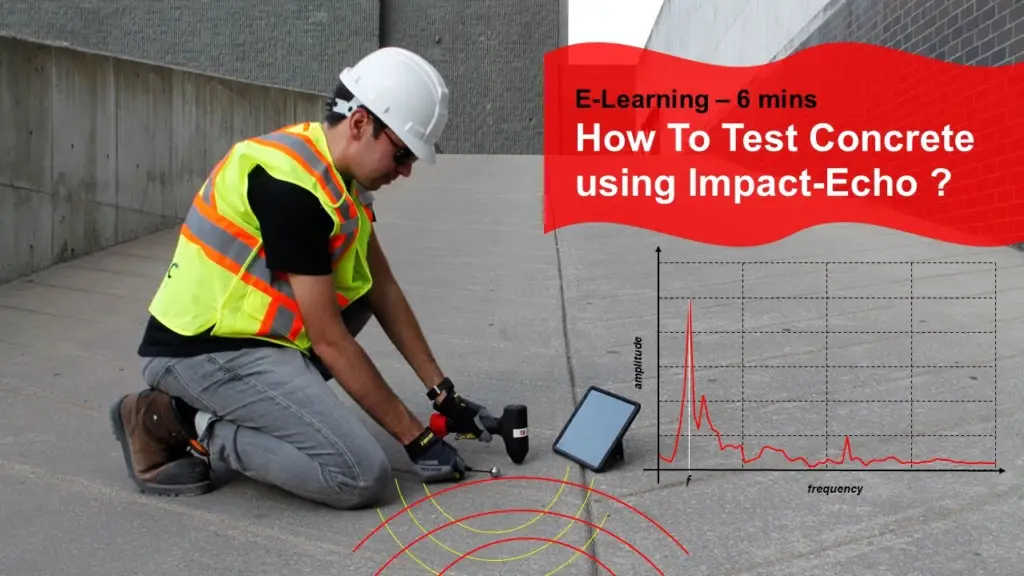
Pull-out Test:
The pull-out test is a non-destructive test that is used to assess the bonding strength between concrete and reinforcing bars or other embedded elements. Tensile force is applied to a tiny cylindrical or conical concrete specimen with a reinforcing bar or other embedded material protruding from it throughout the test. The force necessary to extract the embedded material from the concrete is measured, and the findings are used to calculate the bond strength between the concrete and the embedded material.
Subscribe Us on YouTube!
The pull-out test determines the bond strength between the concrete and the embedding material, which is an important aspect in assessing the structure’s total load-bearing capability. The test findings can be used to assess the efficacy of surface treatments intended to strengthen the binding between the concrete and the embedding material, such as shot blasting or chemical treatments.
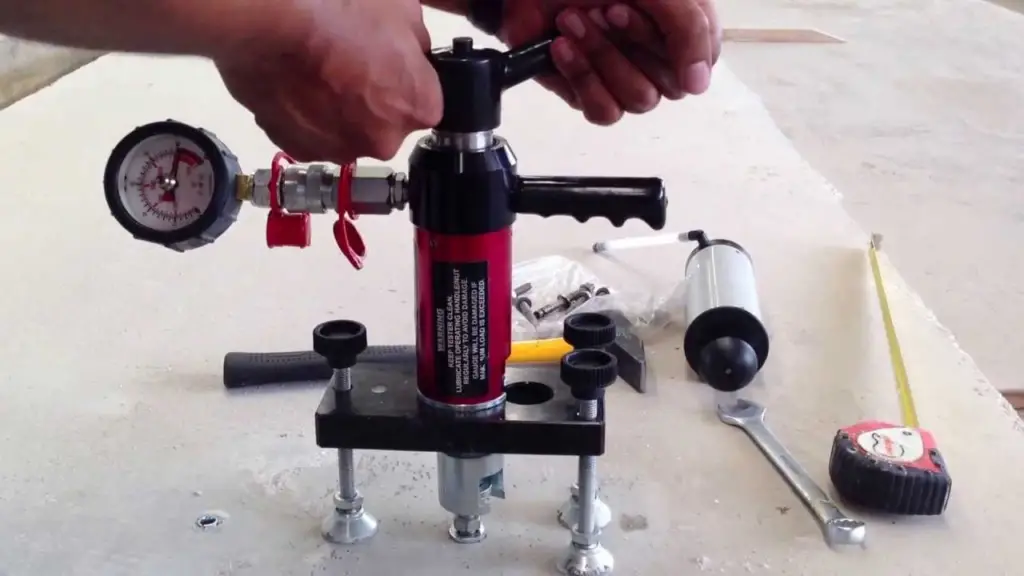
Also Read: Concrete Calculator Triangle (Easy to Use)
Magnetic particle inspection Test:
Cast iron components, welds, and other metal structures are frequently inspected using MPI. Because the process is quick, efficient, and inexpensive, it is a preferred choice for industrial and manufacturing applications. MPI is also used to evaluate concrete buildings with reinforcing steel since it can detect fractures or other faults in the reinforcing steel that could weaken the structure and represent a safety issue.
MPI has the advantage of being able to be done on-site, without the requirement for disassembly or removal of the component being inspected. This makes it a quick and easy way to evaluate massive or complicated structures like bridges or building frames. Surface and near-surface cracks, as well as other flaws, in ferromagnetic materials such as iron or steel. A magnetic field is applied to the material, and then a fine iron oxide or iron oxide-coated magnetic powder is applied to the surface. The magnetic powder attracts areas of flux leakage produced by fractures or other imperfections, allowing the inspector to see the problems.
Also Read: Dry Lean Concrete (DLC) full form – Specification & Construction
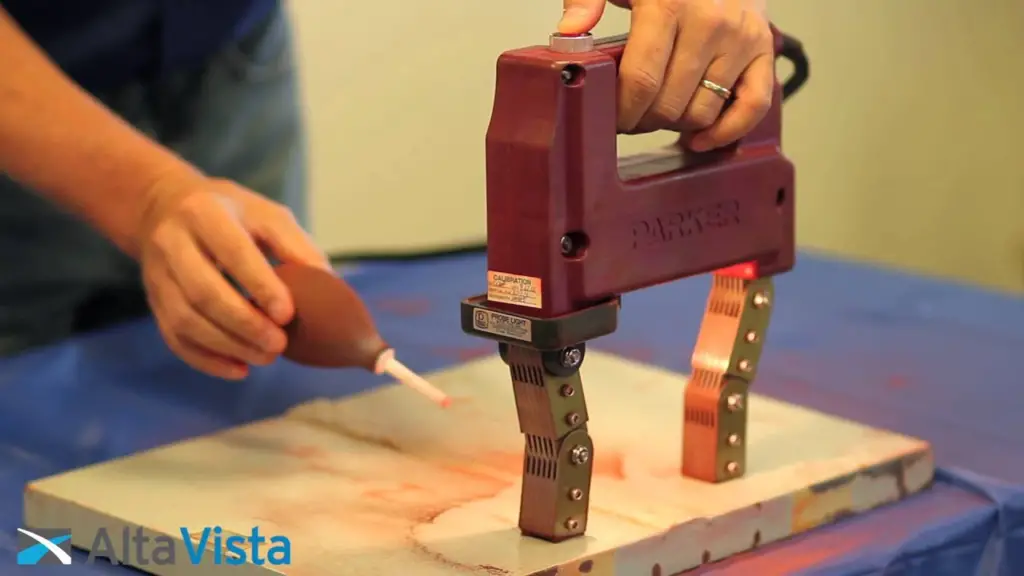
Radiography Testing:
A radiation source is placed on one side of the component being examined, while a radiation detector is placed on the other. The radiation enters the substance and is absorbed to varied degrees depending on its density and composition. This data is then processed to create a visual representation of the internal structure. Internal faults like fractures, porosity, or other discontinuities that might weaken the structure and constitute a safety issue can be detected using RT. It may also be used to check the thickness of concrete buildings and the quality of reinforcing steel and other embedded elements.
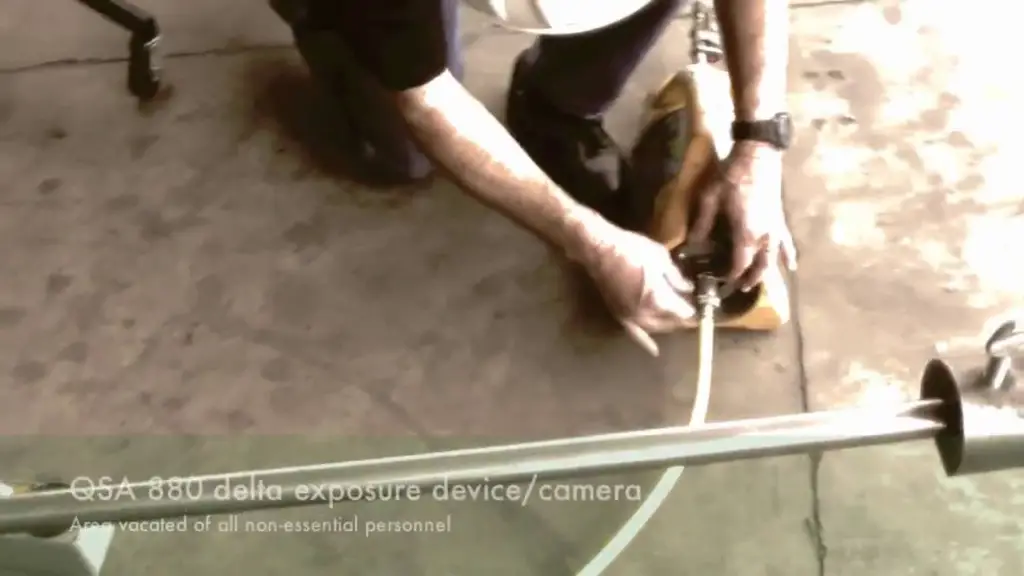
One of the advantages of RT is that it offers detailed photographs of the interior structure of the component, allowing for a thorough evaluation of the material’s state. RT is also adaptable, since it may be used on components of various sizes and forms, including huge or complicated constructions. However, it necessitates specialized equipment and experienced staff, and its usage in particular regions may be restricted due to the risk of ionizing radiation exposure.
Conclusion:
NDT is a valuable technique for assuring the quality and dependability of concrete structures, and it is frequently used in construction and engineering to assess the state of concrete structures such as bridges, buildings, dams, and roads. NDT is a rapid and low-cost approach to examining the integrity and quality of concrete buildings without causing material damage, and it can assist to avoid possible risks and costly repairs. Therefore, non-destructive testing of concrete is an important instrument in the building and engineering sectors for verifying the quality and dependability of concrete structures. There are numerous NDT techniques for concrete, each with its own advantages and disadvantages.