Cement is a very fine substance that is mainly made up of calcium, silicon, bauxite and iron ore. It is a binding material used in concrete for construction that sets, hardens, and adheres to other materials to hold them together. It is manufactured through a controlled chemical combination of limestone, silicon, aluminum, iron and other ingredients. Cement cannot be used on its own, however it is mixed with different material to utilize its full potential which is its phenomenal binding properties. Cement is available in different grades. The ultimate strength of concrete mix is strictly dependent on the class or grade of cement.
In the construction industry, there are different grades of cement used. The main difference between these grades is their binding properties, composition, and use according to ground situation or requirement Any grade of cement shows the compressive strength of that cement. Which is the strength of the cement molded cube after 28 days of curing. The grade of a cement highly affects the strength of any structure.
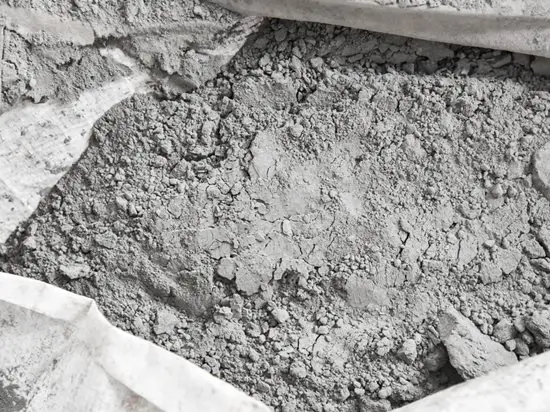
Cement Grades:
Some of the widely used grades of cement available in the market are as follows:
- 33 Grade Cement
- 43 Grade Cement
- 53 Grade Cement
33 Grade Cement:
This is the most common grade cement for general civil construction activities which include plastering, flooring and masonry and it is used up to M20 grade concrete. Grade 33 cement features low compressive strength and low heat of hydration which helps in eliminating cracking related issues. Grade 33 cement is commonly used for smaller residential and commercial construction due to its limited compressive strength. As the name suggests, Grade 33 cement means that the compressive strength of the cement after 28 days is 33 N/mm2. The initial setting time of grade 33 cement is 30 minutes whereas the final setting time is 10 hours.
43 Grade Cement:
Similar to grade 33 cement, grade 43 cement is also used for general civil works like plastering, flooring and masonry and it is used up to M30 concrete grades. The fineness value of the grade 43 grade test by Blain’s air permeability methods that it is not less than 225 m/kg. This cement grade is standard in south Asian countries because of its versatility. In the construction industry, grade 33 cement is used in the making of precasted materials like tiles, pipes, and concrete blocks. Not only that it is also used in concrete work reinforcement, plastering, and flooring.
53 Grade Cement:
The compressive strength of grade 53 cement (10,000 psi) is way more than its predecessors. The weight bearing capacity of grade 53 cement is phenomenal. This is recommended in high scale commercial construction projects. The initial setting time is 30 minutes and final setting time is 10 hours. Grade 53 cement is used in plastering roads, bridges, concrete sleepers of railway, pre-stressed girders, and runways of airports. In the construction industry, when speedy progress is needed grade 53 cement is used.
Compressive Strength Comparison:
Sr. no | Grade of Cement | Compressive Strength in 7 Days N/mm2 | Compressive Strength in 14 Days N/mm2 | Compressive Strength in 28 Days N/mm2 |
1 | Grade 33 | 16 | 23 | 27 |
2 | Grade 43 | 22 | 33 | 37 |
3 | Grade 53 | 33 | 43 | 33 |
Types of Cement:
There are different types of cements that are widely used in the construction industry for different purpose and requirements. Some of them are as follows:
- Ordinary Portland Cement
- Portland Pozzolana Cement
- Rapid Hardening Cement
- Low heat Cement
- Sulfates Resistant Cement
- Quick Setting Cement
Ordinary Portland Cement:
Ordinary Portland Cement (OPC) is a mixture of limestone, argillaceous, calcareous, and gypsum. It emits carbon dioxide during the manufacturing process. It is very suitable for fast construction whereas it is not recommended for mass concreting. OPC comes in grade 33, grade 43 and grade 53. It is used in all general construction. It is also used to make concrete mortars, grouts, and blocks. OPC has easy workability properties and low heat of hydration. It has low resistance against alkalis, sulfates, and chlorides.
Portland Pozzolana Cement:
Portland Pozzolana Cement (PPC) is manufactured the same way as OPC is manufactured with the addition of pozzolanic materials. PPC mixture contains clinkers, gypsum, volcanic ash, and fly ash or silica fumes. It has higher strength than OPC. PPC has a low heat of hydration so it can be used for mass concreting. It is very effective in aggressive weather conditions. It is cheaper than OPC. However, it has a higher setting time than OPC. Portland pozzolana cement has higher resistance against alkalis, sulfates, and chlorides. This is why it is very useful in the construction of dams, bridges, sewage works, marine structures, and piers.
Like Us on Facebook!
Also read: The rate of heat of hydration of the bogue’s compounds
Subscribe Us on YouTube!
Rapid Hardening Cement:
This is the special purpose cement that achieves strength is less. It takes 3 days for rapid hardening cement to achieve the strength that OPC and PPC can achieve in 7 days. This type of cement is not suitable for mass concreting because it emits high heat of hydration. However, it is very applicable in cold weather conditions. It is normally used for the construction of road pavements where we have a time constraint. It is resistant to sulfates attacks. It is recommended for fast pace construction.
Also Read: Effect of Fineness of Cement on Concrete Properties
Low heat Cement:
This type of cement is prepared by keeping the percentage of tricalcium aluminate below 6% and by increasing the percentage of C2S. Low heat cement is used in the construction of dams. It is less reactive to alkali, chlorides and sulfate and has the initial setting time greater than OPC.
Sulfates Resistant Cement:
As the name shows, it is very effective when it comes to Sulphur attacks in concrete. It also has a low percentage of tricalcium aluminate. It is used for construction is involved with soil or groundwater.
Quick Setting Cement:
The strength and specification of quick setting cement are same as OPC; however, it just sets faster than OPC. Quick setting cement is used for underwater construction where quick setting of cement is needed. It can also be used in cold weather and rainy conditions.
Further Read: 9+ Tips For On Site Checking Quality Of Cement