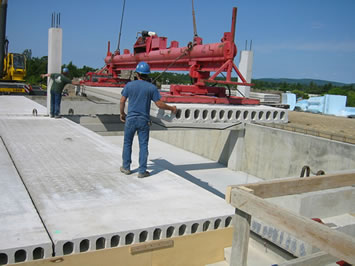
What Is Hollow Core Slab? Uses And Specifications
You might have seen and used hollow blocks for building walls which are very effective as an insulation and light weight partition option. Similarly there is a concept recently introduced as hollow slab or hollow core slabs.
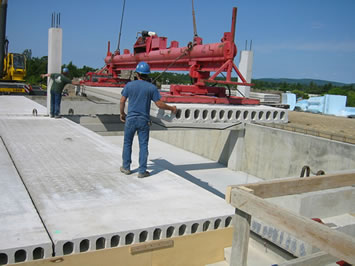
Hollow Core Slabs are actually precast, prestressed concrete slab panels having circular openings throughout the length of the panel. Hollow core slabs are sometimes also termed as Voided Slabs or Concrete Planks. Hollow Core slabs are typically used in construction of floors or roof in a multistory building.
If the area in which you are planning to construct a building is in a low-seismic zones and you want to have a precast concrete construction to ensure fast handing-over of the project than hollow core slab is best suited for your building.
In a typical slab panel, usually four and six no of cores run through in longitudinal direction. The introduction of cores will reduce the weight of the panel and thus of the whole structure. In order to increase the strength of the core slab panels, 12 mm diameter steel strands are introduced that will be prestressed afterwards.
The precast, prestressed hollow core slabs are available in the market in different depths. Currently five basic depths are available like 200, 220, 300, 320 and 400 mm.
Building systems using hollow core slabs have proven to be effective and efficient in residential buildings, schools, hospital, parking plazas and all types of multistory buildings.
Advantages
Hollow Core slabs have numerous advantages over typical slab system, some of these advantages are as follows:-
Fast Construction
As the slabs are precast and are mostly casted in automated factories where there is no requirement of large no of labors and also no formwork and shuttering cost is required. There is no wastage of time in curing and waiting for the slab to get its strength before removal of formwork. This reduces the construction cost.
Increased Workmanship Standard
As the labor required is only for fixing of the panels and not of the pouring thus, site problems like honey combing due to poor vibration of the concrete mass, segregation and bleeding due to excessive vibration can be avoided which will improve the quality and life of the structure.
Light weight Structure
As the core of the hollow slab have holes and voids which run throughout the panel thus it reduces the material i.e. concrete and thus reduces the overall weight of the structure. This light weight will be considered in the design thus reducing the cross-sections which will ensure ultimate economical construction.
No need of plastering or finishing underside
As the hollow slab is pre-cast and is usually casted in factories the finishes is always smooth and cleaned and thus there is no need to plaster the underside of the slab to achieve smooth and finished ceiling. You can directly apply the paints and acoustical sprays.
Fire Resistance
The voids of the slab have air within it and as there will be no medium for the fire to transfer thus better insulation of the fire exists which not only will ensure to maintain the inner temperature but will also remain cool in summers.
Use of Voids as Electrical Conduits
In case of buildings we all know that the HVAC and other ducts like electrical supply, gas supply pipes and other utility pipes needed to be embedded within the walls and the roof. In traditional building slabs the small conduits are needed to be placed in order to run the wires within it. But in precast hollow core slabs this is premade.
Usually 200 meter panels of slab are made by a process called extrusion in which wet concrete along with prestressed steel wire rope is poured which are afterwards cut with a big diamond circular saw as per the required length and width.
Sometimes the hollow core slab is not prestressed in such cases they are made on carousel production lines which are directly made of the exact length as required. The length of such a slab is limited to 7 to 8 meters. This system of construction is very famous in Belgium where it is widely used in private house projects.
Due to reduced thickness the hollow core slab might face a problem; i.e. sound of foot steps which might be very irritating sometimes. In such cases, to ensure soundproofing floor needs to be covered with a soft floor covering or floor screed should be poured or even a strip of rubber will do the work.